How To Choose The Right Silicone Conformal Coating For PCB Protection In 2025
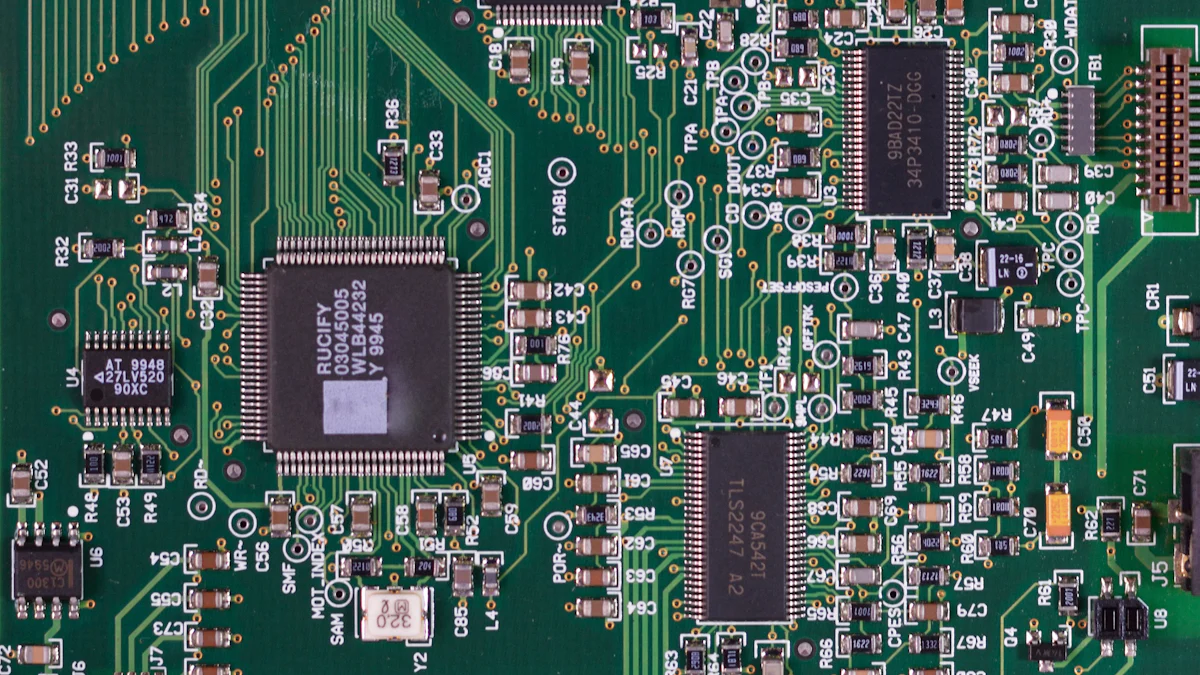
Protecting PCBs from environmental damage is more critical than ever. Silicone conformal coatings play a vital role in shielding these components from moisture, extreme temperatures, and chemical exposure. They ensure electronic devices remain reliable, even in harsh conditions. Did you know these coatings can endure temperatures ranging from -60°C to 200°C? That’s why they’re a go-to solution for rugged environments.
When choosing the right silicone conformal coating for PCB in 2025, you’ll want to focus on material properties, application methods, and certifications. These coatings not only resist corrosion but also prevent issues like tin whiskers and condensation. Staying informed about innovations, like TaC coatings or tac ceramic coating, can help you make smarter decisions for your PCB protection needs.
Key Takeaways
- Silicone coatings keep PCBs safe from water, heat, and chemicals.
- Pick a coating with flexibility, water resistance, and heat protection.
- Learn about new options like TaC coatings and eco-friendly choices.
- Use brushing, spraying, or dipping based on your project needs.
- Certifications like IPC-CC-830B and UL94 prove safety and quality.
Understanding Silicone Conformal Coatings
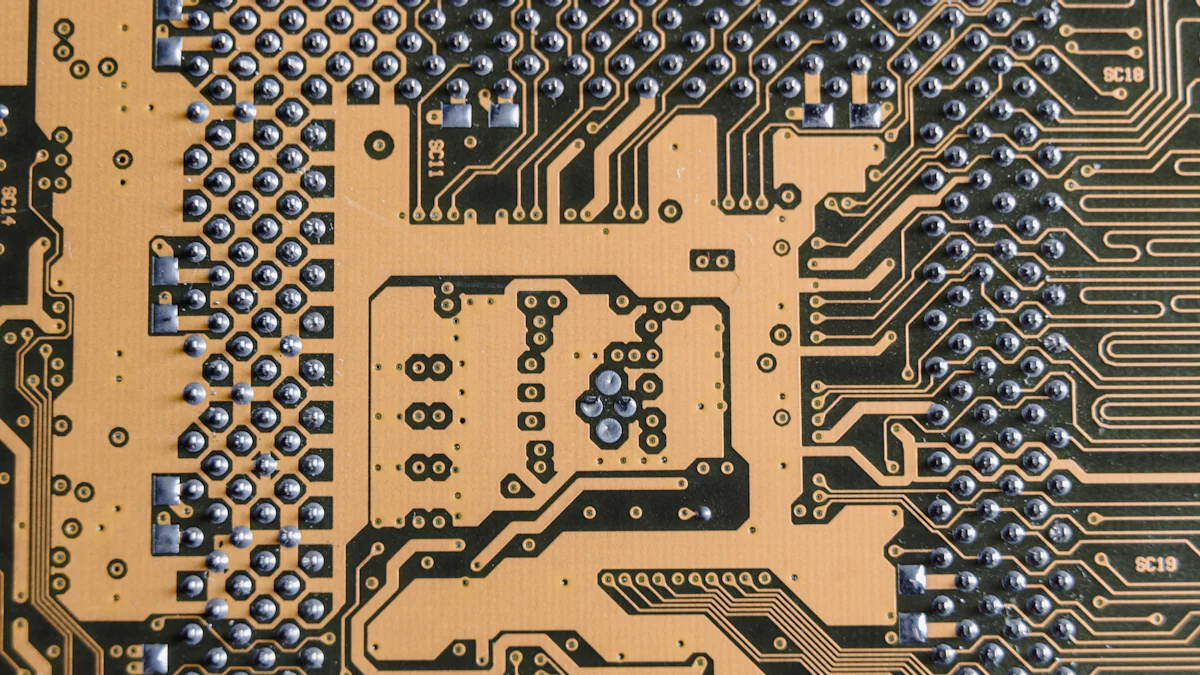
What Are Silicone Conformal Coatings?
Let’s start with the basics. Silicone conformal coatings are protective layers applied to printed circuit boards (PCBs). They’re designed to shield sensitive components from environmental factors like moisture, dust, and extreme temperatures. These coatings are made from silicone-based materials, which are known for their flexibility and durability.
Here’s what makes them stand out:
- They resist moisture and fungal growth.
- They provide excellent electrical insulation.
- They can handle high temperatures, often exceeding 120°C.
- They’re elastic, which helps reduce mechanical or thermal stress.
- They meet strict industry standards like IPC-CC-830B and UL Standard 746E.
Silicone coatings also retain their elasticity after curing, making them ideal for protecting PCBs in dynamic environments.
Benefits of Silicone Coatings for PCB Protection
Why should you choose silicone coatings for your PCBs? The benefits are hard to ignore. First, they’re incredibly resistant to moisture and corrosion. This means your PCBs stay safe even in humid or wet conditions. Second, they can handle extreme temperatures, from freezing cold to scorching heat.
Here’s a quick look at their advantages:
Benefit | Description |
---|---|
Moisture Resistance | Hydrophobic silicone prevents water absorption, mitigating corrosion risks. |
Temperature Handling | Endures heat up to 200°C and cold down to -60°C, suitable for extreme climates. |
Flexibility & Shock Absorption | Elastic silicone dampens vibrations and cushions against mechanical damage. |
Chemical Resistance | Offers broad resistance to fuels, oils, and cleaning agents, with limited degradation from strong acids/bases. |
These coatings also provide excellent adhesion to PCB surfaces, ensuring long-lasting protection. Plus, they’re non-flammable, adding an extra layer of safety.
Common Applications in Electronics
Silicone conformal coatings are everywhere. You’ll find them in industries like automotive, medical, and consumer electronics. For example:
- Automotive Applications: They protect PCBs in vehicles from moisture and abrasion.
- Medical Devices: Silicone coatings ensure durability in devices exposed to heat and moisture.
- Industrial Electronics: They shield machinery electronics from shocks and solvents.
- Wearable Devices: These coatings guard against spills and moisture in personal gadgets.
In advanced applications, TaC coatings are also gaining attention for their unique properties. While silicone remains a top choice for PCB protection, innovations like these are worth keeping an eye on.
Key Factors for Choosing the Right Coating
Choosing the right silicone conformal coating can feel overwhelming, but breaking it down into key factors makes it easier. Let’s dive into what you should look for.
Material Properties
Thermal Resistance
When it comes to thermal resistance, silicone coatings stand out. They can handle temperatures as high as 200°C (400°F) without breaking a sweat. This makes them perfect for electronics exposed to extreme heat, like automotive or industrial applications. Plus, they retain their elasticity even after curing, which helps protect against mechanical stress caused by temperature changes.
Electrical Insulation
Silicone coatings are excellent insulators. They prevent electrical shorts by creating a barrier between components. This is especially important for high-voltage circuits or devices operating in humid environments. You’ll want a coating that maintains its insulating properties over time, even when exposed to moisture or contaminants.
Flexibility and Durability
Flexibility is a game-changer. Silicone coatings stay elastic, which means they can absorb vibrations and mechanical shocks without cracking. This is why they’re often used in aerospace and marine applications. Their durability ensures long-term protection, even in challenging conditions.
Environmental Resistance
Protection Against Moisture and Humidity
Moisture is a PCB’s worst enemy. Silicone coatings are hydrophobic, meaning they repel water and prevent corrosion. This makes them ideal for humid environments or devices exposed to condensation.
Resistance to Chemicals and UV Exposure
Silicone coatings also resist chemicals like fuels, oils, and cleaning agents. They hold up well under UV exposure, making them suitable for outdoor applications. Whether it’s a solar panel or a wearable device, these coatings provide reliable protection.
Compatibility with PCB Components
Avoiding Material Interactions
Compatibility is crucial. Some coatings can interact with PCB materials, causing issues like solvent entrapment or cure inhibition. For example, contaminants from flux or skin oils can prevent silicone from curing properly. Always ensure surfaces are clean before applying the coating.
Ensuring Adhesion to PCB Surfaces
Good adhesion is non-negotiable. Silicone coatings bond well with most PCB materials, but overapplication can lead to drips or excess buildup. This might interfere with enclosures or other components. Proper application techniques can help avoid these pitfalls.
By focusing on these factors, you can choose a coating that meets your needs. And while silicone remains a top choice, innovations like TaC coatings are worth exploring for advanced applications.
Silicone Coatings vs. Other Coating Types
Silicone vs. Acrylic Coatings
When comparing silicone and acrylic coatings, I always think about the environment the PCB will face. Silicone coatings shine in high-temperature applications. They can handle extreme heat without breaking down, unlike acrylic coatings, which tend to degrade under similar conditions. Silicone’s flexibility is another big win. It bends and stretches without cracking, making it perfect for devices that experience thermal expansion or vibrations.
Here’s why silicone coatings often come out on top:
- High-temperature resistance: Silicone handles heat better than acrylic.
- Flexibility: Silicone stays elastic, while acrylic can become brittle.
- Moisture protection: Silicone offers superior moisture resistance, ideal for humid or outdoor environments.
Acrylic coatings do have their place, especially when cost is a concern. But for long-term reliability, silicone is hard to beat.
Silicone vs. Urethane Coatings
Silicone and urethane coatings both offer solid protection, but they perform differently. Silicone coatings are much more flexible. They stretch and move with the PCB, which is crucial for applications where components shift or vibrate. Urethane, on the other hand, can become rigid over time.
Durability is another area where silicone wins. It lasts about three times longer than urethane, especially in harsh conditions. Silicone resists UV light, moisture, and extreme temperatures, while urethane often fails under prolonged UV exposure. If you’re looking for a coating that can handle movement and tough environments, silicone is the way to go.
Silicone vs. Epoxy Coatings
Silicone and epoxy coatings each have their strengths, but they’re suited for different needs. Let me break it down for you:
Feature | Silicone Coatings | Epoxy Coatings |
---|---|---|
Flexibility | Retains elasticity, good for vibrations | Hard and brittle, less flexible |
Moisture Resistance | Excellent resistance against moisture and corrosion | Strong resistance to humidity |
Chemical Resistance | Good resistance to chemical contamination | Strong resistance to chemicals |
Temperature Resistance | Manages temperatures up to 400°F (200°C) | High-temperature resistance, but not as great as silicone |
Adhesion | Good adhesion properties with PCB materials | Greater adhesion strength than silicones |
Removal Difficulty | Easier to remove | Difficult to remove |
Silicone coatings are more versatile. They’re easier to remove and better for applications requiring flexibility. Epoxy coatings, however, excel in adhesion and chemical resistance. If you need a robust, permanent solution, epoxy might be the better choice. But for dynamic environments, silicone is the clear winner.
By understanding these differences, you can choose the right coating for your specific needs. And don’t forget to explore innovations like TaC coatings, which are making waves in advanced applications.
Silicone vs. Parylene Coatings
When it comes to silicone and parylene coatings, each has its strengths. But let me tell you, they’re quite different in how they perform and where they shine. Silicone coatings are like the all-rounders of PCB protection. They cure quickly, which saves time during production. They also handle vibrations and shocks like a pro, especially when applied in thicker layers. If you’re dealing with extreme temperatures or UV exposure, silicone coatings are your best bet. They stick well to PCB materials and are easy to rework if repairs are needed.
Parylene coatings, on the other hand, are all about precision. They’re applied in ultra-thin, uniform layers through a vapor deposition process. This makes them perfect for applications where space is tight, like microelectronics or medical devices. Parylene offers excellent moisture resistance and dielectric properties. However, it’s not as flexible as silicone. It can crack under mechanical stress or vibrations. Plus, removing parylene for repairs is a real challenge.
Here’s a quick comparison to make it clearer:
Feature | Silicone Coatings | Parylene Coatings |
---|---|---|
Application Thickness | Can be applied thickly for shock absorption | Ultra-thin, uniform layers |
Flexibility | Highly elastic, absorbs vibrations | Rigid, prone to cracking under stress |
Thermal Resistance | Excellent, handles extreme temperatures | Limited compared to silicone |
Reworkability | Easy to repair or remove | Difficult to remove |
UV and Corrosion Resistance | Outstanding | Moderate |
If you need flexibility, durability, and ease of repair, silicone coatings are the way to go. But if you’re working with delicate, space-constrained designs, parylene might be worth considering.
Relevance of TaC Coatings in Advanced Applications
Now, let’s talk about TaC coatings. These are making waves in advanced applications, and for good reason. TaC coatings, or tantalum carbide coatings, bring exceptional hardness and wear resistance to the table. They’re perfect for industries like semiconductors and photovoltaics, where durability and precision are critical.
I’ve noticed that TaC coatings excel in environments where traditional coatings might fall short. For example, they can withstand extreme heat and chemical exposure without breaking down. This makes them ideal for high-performance electronics or devices exposed to harsh conditions. While silicone coatings remain a top choice for general PCB protection, TaC coatings are carving out a niche in cutting-edge technologies.
If you’re exploring advanced applications, it’s worth keeping an eye on TaC coatings. They might just be the next big thing in PCB protection.
Application and Curing Techniques
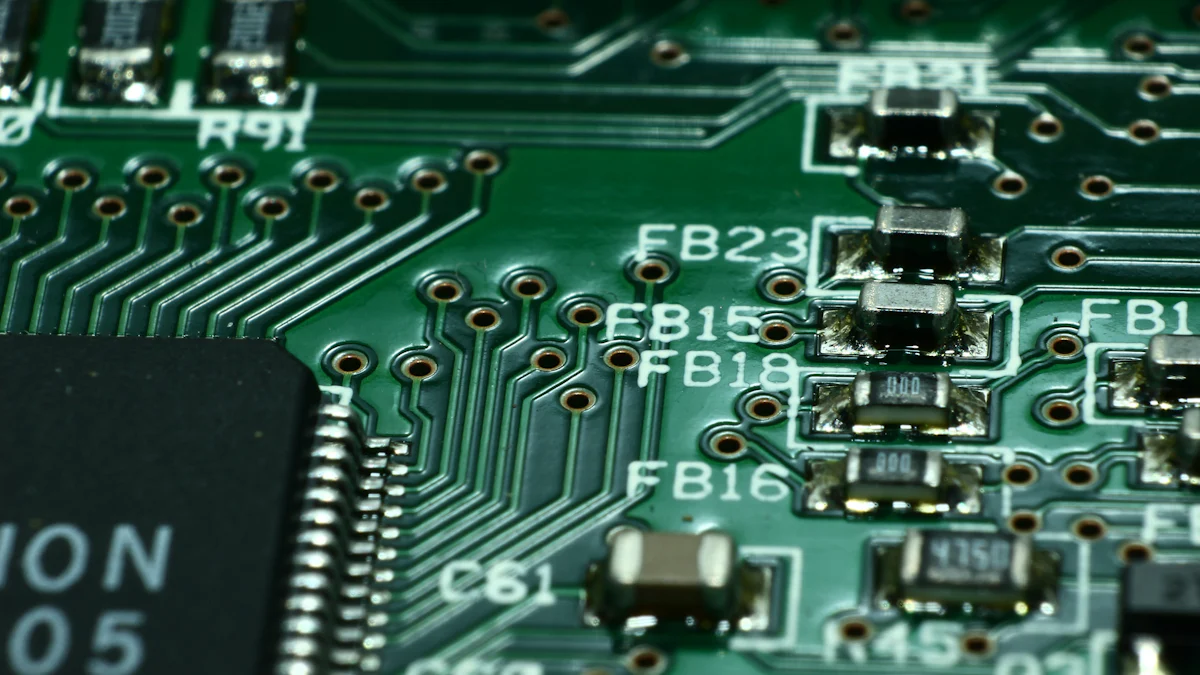
When it comes to applying silicone conformal coatings, the method you choose can make a big difference. Each technique has its strengths, and picking the right one depends on your project’s needs. Let me walk you through the most common methods.
Application Methods
Brushing
Brushing is the simplest way to apply silicone coatings. You use a brush to spread the coating over the PCB. It’s great for small repairs or touch-ups. However, it’s not the fastest method. It works best for small batches or when precision is key. If you’re working on a single board or fixing a specific area, brushing gets the job done.
Spraying
Spraying is a popular choice for many. You can use an aerosol can or a handheld spray gun to apply the coating. It’s quick and works well for low-volume production. For larger projects, selective coating with robotic spray nozzles is a game-changer. It targets specific areas, saving time and reducing waste. Spraying gives you a smooth, even layer, which is perfect for consistent protection.
Dipping
Dipping involves immersing the entire PCB into a coating solution. It’s practical for coating both sides of the board at once. However, you’ll need to mask off areas that shouldn’t be coated. This method is efficient for medium to high-volume production. It ensures thorough coverage, especially for complex designs.
Here’s a quick comparison of these methods:
Application Method | Description |
---|---|
Manual Spraying | Applied using an aerosol can or handheld spray gun; suitable for low-volume production. |
Selective Coating | Automated process using robotic spray nozzles for specific areas; ideal for high-volume production. |
Dipping | Immerses the board in coating solution; requires masking and is practical for both sides of the board. |
Brushing | Simple technique for repairs; labor-intensive and best for small batches. |
Curing Processes
Once the coating is applied, curing is the next step. This process solidifies the coating, ensuring it adheres properly and provides lasting protection. Let’s explore the three main curing methods.
Room-Temperature Curing
Room-temperature curing is the easiest option. You just let the coating dry naturally at ambient temperature. It’s energy-efficient and doesn’t require special equipment. However, it takes longer—sometimes up to 24 hours. This method works well for small-scale projects or when time isn’t a constraint.
Heat Curing
Heat curing speeds things up. You place the coated PCB in an oven, where heat accelerates the curing process. This method is ideal for high-volume production. It ensures consistent results and reduces curing time significantly. If you’re in a hurry or need a durable finish, heat curing is a solid choice.
UV Curing
UV curing is the fastest method. It uses ultraviolet light to harden the coating in seconds. This technique is perfect for automated production lines. It’s efficient and delivers a high-quality finish. However, it requires specialized equipment and UV-curable coatings. If speed and precision are priorities, UV curing is worth considering.
Each method has its place. Whether you’re brushing on a small repair or using UV curing for mass production, the right technique ensures your PCBs stay protected.
Certifications and Compliance for 2025
Importance of Certifications for PCB Coatings
Certifications matter more than you might think when it comes to silicone conformal coatings. They’re not just fancy labels—they’re proof that a coating meets strict safety and performance standards. In 2025, with electronics becoming even more advanced, these certifications ensure your PCBs stay protected and reliable.
Here’s a quick breakdown of why certifications are so important:
Certification | Purpose | Importance |
---|---|---|
IPC-CC-830B | Distinguishes engineered coatings for PCB protection | Ensures safety and performance standards |
UL746E | Evaluates flammability using UL94 standard | Indicates low flammability potential (V-0 rating) |
Think of certifications as a seal of trust. They tell you that the coating has been tested for things like insulation, flammability, and durability. Without them, you’re taking a gamble on your PCB’s safety and performance.
Key Standards to Consider
When choosing a silicone conformal coating, you’ll want to look for specific standards. These standards act as a checklist to ensure the coating performs as expected. Let me walk you through the key ones.
IPC-CC-830B
This is the go-to standard for conformal coatings. It tests for things like appearance, insulation resistance, and flammability. If a coating meets IPC-CC-830B, you know it’s built to last. It’s like a stamp of approval for quality and reliability.
UL94 (Flammability Standards)
Flammability is a big deal, especially for electronics. UL94 tests how a coating reacts to fire. A V-0 rating means the coating is highly resistant to flames, which is exactly what you want for safety. Silicone coatings often excel here, making them a smart choice for critical applications.
RoHS and REACH Compliance
In 2025, eco-friendliness isn’t optional—it’s essential. RoHS (Restriction of Hazardous Substances) and REACH (Registration, Evaluation, Authorization, and Restriction of Chemicals) ensure coatings are free from harmful substances. These certifications show that the coating is safe for both people and the planet.
By sticking to these standards, you can feel confident in your choice. They’re like a roadmap to finding the best silicone coating for your PCB.
Emerging Trends and Innovations
Advances in Silicone Coating Formulations
Silicone coatings have come a long way. Today, they’re tougher, more flexible, and better suited for demanding environments. For instance, Miller-Stephenson’s Silicone Conformal Coating uses advanced silicone technology to deliver exceptional moisture resistance and dielectric properties. It’s perfect for high-temperature and high-vibration applications, extending the life of PCBs.
Here’s what makes these new formulations stand out:
- High-temperature resistance: They thrive in extreme heat, making them ideal for automotive or industrial electronics.
- Flexibility: They bend and stretch without cracking, even during thermal expansion.
- Moisture protection: Hydrophobic properties keep water out, reducing corrosion risks.
Some popular options include Humiseal 1C49 and Dow Corning 3-1965, both known for their reliability in harsh conditions. These coatings don’t just protect; they enhance the performance and durability of PCBs.
Tip: If your PCBs face high heat or vibrations, look for coatings designed with these advanced features.
Eco-Friendly and Sustainable Coating Solutions
Sustainability is a big deal in 2025. Many companies are now offering eco-friendly silicone coatings that protect PCBs while being kind to the planet. For example, Elemax™ Air & Water Resistive Barrier coatings are 100% solvent-free and alkoxy silicone-based. They create a seamless barrier against water but still let vapor escape.
These coatings do more than protect. They improve insulation and help control internal temperatures, cutting energy use by up to 35%. Plus, they support sustainability goals like LEED and Net Zero Emissions.
Here’s why they’re worth considering:
- Energy efficiency: Reduced energy consumption means lower costs and a smaller carbon footprint.
- Environmental compliance: They align with green building standards and eco-friendly initiatives.
Note: Choosing sustainable coatings isn’t just good for the environment—it’s good for your bottom line too.
Enhanced Application Technologies
Application methods are evolving fast. New technologies are making it easier to apply silicone coatings with precision and efficiency. Nano-coatings, for example, offer superior protection with ultra-thin layers. These are especially useful in aerospace and medical devices, where space and weight are critical.
Automated coating systems are another game-changer. They ensure consistent application, reduce waste, and speed up production. Whether you’re working on a small batch or a large-scale project, these systems save time and improve quality.
Here’s what’s new:
- Nano-coatings: Minimal thickness, maximum protection.
- Advanced materials: Tailored for specialized industries like aerospace.
- Automation: Faster, more accurate, and less wasteful.
Pro Tip: If you’re scaling up production, consider investing in automated systems for better results.
Emerging trends like these are shaping the future of PCB protection. Staying updated can help you make smarter choices for your projects.
Integration with Smart Manufacturing Processes
Smart manufacturing is changing the game for silicone conformal coatings. I’ve seen how factories are now using advanced technologies to make production faster, more precise, and efficient. It’s not just about applying coatings anymore—it’s about doing it smarter. Let me show you how this works.
1. Automation and Robotics
Automation is a big deal in modern factories. Machines now handle tasks like spraying or dipping PCBs with silicone coatings. Robots can apply coatings with pinpoint accuracy, reducing waste and ensuring every board gets the same level of protection. This consistency is a game-changer for high-volume production.
Tip: If you’re scaling up, consider automated systems. They save time and cut down on errors.
2. IoT-Enabled Monitoring
The Internet of Things (IoT) is making factories smarter. Sensors track every step of the coating process. They monitor things like temperature, humidity, and curing times. If something goes wrong, the system alerts the operator immediately. This means fewer mistakes and better quality control.
3. Data-Driven Decisions
Smart manufacturing relies on data. Machines collect tons of information during production. This data helps identify trends, predict maintenance needs, and improve efficiency. For example, if a coating machine starts slowing down, the system can flag it before it causes delays.
Smart Manufacturing Feature | Benefit |
---|---|
Automation | Faster production, reduced waste, and consistent quality |
IoT Monitoring | Real-time tracking and immediate alerts for better quality control |
Data Analytics | Predictive maintenance and process optimization |
Smart manufacturing isn’t just a trend—it’s the future. By integrating these technologies, companies can produce better coatings faster and with less waste. If you’re in the PCB industry, now’s the time to embrace these innovations. They’ll keep you ahead of the curve.
Note: Investing in smart manufacturing might seem costly upfront, but the long-term benefits are worth it.
Choosing the right silicone conformal coating for PCB protection isn’t just a technical decision—it’s about ensuring reliability and durability in challenging environments. These coatings stand out because they retain elasticity after curing, resist moisture and corrosion, and adhere well to PCB surfaces. They’re perfect for industries like aerospace, marine, and automotive, where extreme conditions are the norm.
Here’s a quick recap of what to look for:
- Flexibility: Protects against vibrations and mechanical stress.
- Moisture Resistance: Keeps PCBs safe in humid or wet conditions.
- Temperature Tolerance: Handles up to 400°F (200°C) with ease.
Emerging trends, like coatings rated for even higher temperatures and eco-friendly solutions, are reshaping the industry. Staying informed about these innovations can help you make smarter choices. So, whether you’re protecting consumer electronics or industrial systems, the right coating makes all the difference.
Tip: Keep an eye on advancements in application techniques and sustainable materials—they’re the future of PCB protection!
FAQ
What is the best way to apply silicone conformal coatings?
The best method depends on your project. For small repairs, brushing works well. Spraying is great for even coverage, while dipping ensures thorough protection for complex designs. I recommend spraying for most cases—it’s quick and gives a smooth finish.
How long does it take for silicone coatings to cure?
Curing time varies by method. Room-temperature curing can take up to 24 hours. Heat curing speeds it up to a few hours, while UV curing finishes in seconds. If you’re in a rush, UV curing is the fastest option.
Can silicone coatings handle extreme temperatures?
Absolutely! Silicone coatings thrive in extreme conditions. They can withstand temperatures from -60°C to 200°C. This makes them perfect for automotive, aerospace, and industrial applications where heat or cold is a concern.
Are silicone coatings eco-friendly?
Many silicone coatings now meet eco-friendly standards like RoHS and REACH. Some are even solvent-free, reducing environmental impact. If sustainability matters to you, look for coatings labeled as environmentally compliant.
How do I ensure good adhesion to PCB surfaces?
Cleanliness is key! Make sure the PCB is free of dust, oils, or flux residues before applying the coating. A clean surface ensures strong adhesion and long-lasting protection. I always recommend using isopropyl alcohol for cleaning.